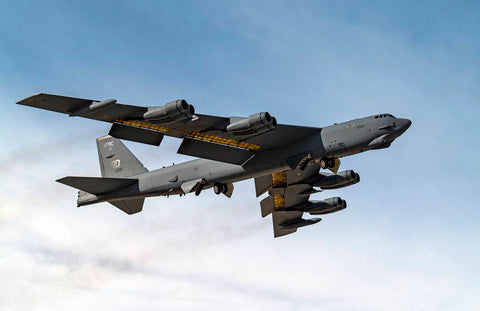
How To Re-Engine a B-52 and Make A New Bomber Fleet
The U.S. Air Force’s rollout of its new B-21 Raider stealth bomber in December was just one piece of the puzzle in creating a future two-bomber fleet. The biggest changes are yet to come.
Rolls-Royce and Boeing are working on a major upgrade to the service’s fleet of 76 Cold War-era B-52 Stratofortresses that will give them a new slate of F130 engines and keep them flying into the 2050s, alongside at least 100 B-21s.
And at some point in the 2030s, when the combined Raider-Stratofortress bomber fleet is ready, the Air Force will finish retiring the remaining B-1 Lancers — originally made by Rockwell International, which is now part of Boeing — and its Northrop Grumman-made B-2 Spirits.
In charge of steering the majority of that effort is Brig. Gen. William Rogers, the program executive officer for the Bombers Directorate at the Air Force Life Cycle Management Center on Wright-Patterson Air Force Base in Ohio. Development of Northrop Grumman’s B-21 is handled by the Air Force’s Rapid Capabilities Office, but managing the entire life cycle of the rest of the bomber fleet falls under Rogers’ purview.
That includes organizing how the Boeing-made B-52 will obtain its new engines under the $2.6 billion Commercial Engine Replacement Program; continuing and perfecting the development of the engines; figuring out where the work will be done when the engines are ready; and working with Air Force Global Strike Command to eliminate capability gaps as engines are swapped out.
The Commercial Engine Replacement Program recently finished its preliminary design review, Rogers said, and he hopes it will get through the Milestone B review — which will mark the completion of its technology maturation phase and begin the engineering and manufacturing development phase — no later than the fourth quarter of fiscal 2023.
Rogers’ office is working with other parts of the Air Force to prepare to retire the B-1 and B-2 fleets, and make sure those airplanes — and their highly sensitive technology — are responsibly handled, whether by destroying them, recycling them or sending them to the boneyard.
But keeping the B-52 fleet flying until they’re nearly a century old isn’t easy. And with their current TF33 engines, made by Pratt & Whitney and dating back to the early 1960s, expected to reach the end of their life spans by the close of the 2020s, there’s a lot riding on this process.
Rogers spoke with Defense News on Dec. 9. This interview was edited for length and clarity.
Does the Air Force still plan to install new engines on B-52s as part of
the bombers’ regularly scheduled depot maintenance?
We’re still refining the acquisition strategy, but that is a very likely course of action. Part of this is also working with the depot [at Tinker Air Force Base in Oklahoma] to make sure they have the bandwidth to do it. Because with B-52, there’s a radar modernization program, there’s the re-engining, there are many other modifications and upgrades that we’re doing, and we’re trying to make sure everything aligns. Our preferred choice is to go through the depot, but we also have other fallback plans, like ordering contractor installation if the depot doesn’t have the bandwidth.
We’re not just looking at giving it to Boeing [if Tinker doesn’t have the capacity]. We’ll look at a variety of options. That’s something we’re working as part of our acquisition strategy. We would like to have a solid feeling [on the plan] by the end of FY23.
What goes into making that decision?
It’s projecting our normal planned depot maintenance, or PDM, and working with the Air Force Sustainment Center to figure out whether we have the space. Could we add a line to do our modernization efforts? What does that look like? How long will it take to establish? How much will it cost? Do they have the workforce to execute it?
I’m not sure we’ve actually decided that we’ll do it as part of the PDM line versus having a separate line, but that’s something we’re trying to figure out now.
As B-52s go into the re-engining process, how do you ensure there isn’t a
significant operational gap?
We work very closely with Air Force Global Strike Command and make sure that we properly time the inductions, flying the aircraft from an operational unit to the depot. At times, we adjust that and may delay to make sure that we don’t induce a gap, especially if there’s a delay in a new aircraft hitting the wing. We try to time it as close as possible for a 1-for-1 trade — as one comes out, one enters.
How did creating a digital twin for the new engine help with the project?
When you build something like that, it helps you iterate and put more rigor into the actual design. The engine itself is designed, but the other pieces of the modification are being newly designed to accommodate that engine. It allows us to iterate and try to find that best design — keep looking at it from different angles, making adjustments and doing it digitally before you manufacture something; “bending metal,” is what we like to say.
[The digital twin also makes it easier to organize] your sustainment documentation and understand how everything fits together. And you can help flow all those diagrams and those detailed drawings down into the hands of those who will eventually one day maintain and operate the aircraft.
Having the testers involved in the process, seeing the model as it’s being developed, building their confidence in what the capability or system can deliver from a capability perspective, and understanding all the pieces — that’s another area in which we hope to benefit, especially on the developmental test side. They understand and can simulate and do things with that model, like figure out how it fits and prove it out, and hopefully accelerate the test at the end of the day. [There are cost savings compared to] actually flying some of those test planes.
Has it helped catch problems before metal starts getting bent?
Yes. [Boeing] has done some demonstrations of how they can look at how things are fitting together better, where before they had to build out the prototype or build the piece. With the digital aspect, you’re able to fine-tune and look at those in a model sense. In the old days, they would pen and ink it, they were using paper. Now you have the model, so you can adjust it digitally, versus doing it on paper and then building to prove it.
A B-2 Spirit bomber taxis at a Royal Australian Air Force
Base on July 25, 2022. (Tech. Sgt. Dylan Nuckolls/U.S. Air Force)
Are we still looking at 2031 or 2032 for the B-1 and B-2 retirements?
They’re going to be event-driven based on how the B-21 fields. I view my job, when it comes to those platforms, as helping the Air Force make smart decisions on what we need to keep them operationally available and relevant. Our adversaries aren’t going to wait for us to have a perfect fleet of B-21s fielded if they decide to do something.
Sometime in the 2030s is typically what we hear, but I don’t have the team focused on divestiture yet. We do work with Air Force Materiel Command to do some early planning along those lines, but it’s really early planning at this point because we don’t have a set plan on when or how we want to retire those aircraft.
The B-2 may have some special consideration for retirement, [such as the bomber’s] low-observable nature and technology that are on some of those aircraft. We still want to make sure some of the technology is protected appropriately, and then also any environmental impacts is the other big category. The Air Force hasn’t decided exactly what [retirement] entails, whether it’s destruction, recycling or storing. There’s a gamut of different ways the Air Force could go. If we have a crew destroying or recycling the aircraft, there are some technologies — in the shapes, the coatings — that we have to protect. We have to think through all those different angles to make sure we do it the right way, when and if that day comes.
Originally published by Military Times, our sister publication.